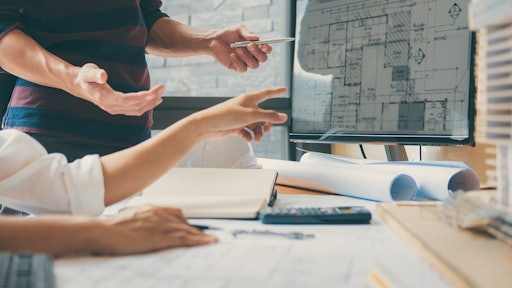
Before the first excavator breaks ground or the first beam is laid, construction projects require extensive planning and preparation during the preconstruction phase. This critical stage lays the groundwork and sets the trajectory for the entire endeavor, establishing the schedules, budgets, and foundational elements upon which success will be built.
For major construction projects, the preconstruction phase can span months or even years, depending on the complexity. While eager stakeholders may be tempted to expedite this process, sufficient time and diligence in preconstruction is invaluable. The work completed during this period will dictate priorities, prevent wasted efforts, uncover cost savings, and minimize risks over the course of the project.
In essence, a solid preconstruction phase is the backbone of any construction undertaking, and a reported 23% of companies reported increased productivity when their preconstruction process was improved.
Realistic cost estimation and budgeting
One fundamental preconstruction task is to develop accurate cost estimates and budgets, and the most important prerequisite here is to have access to all detailed project files and blueprints within one’s estimation toolkit. This process involves more than number-crunching, and requires gaining an intimate understanding of the financial landscape of the project. Meticulous analysis of the needed materials, labor, equipment, and other resources is essential. And yet only 35 % of general contractors reported having dedicated technology to create and manage bids. The goal is to create a budget that is not just correct on paper, but also practical and actionable, and is streamlined to save everyone time.
Here are some key considerations for precise cost estimation and budgeting in construction:
Cost estimation
- Analyzing required materials, labor, and equipment is the starting point. Determining the exact quantities and types of physical resources needed informs cost projections.
- Market research provides indispensable data on current pricing for materials and labor rates in the project's location. This enables estimators to make realistic cost estimates based on present-day figures.
- Past projects with similar specifications and scope serve as handy references for comparison. Historical data helps estimators understand typical costs and make proper adjustments for inflation or market fluctuations.
- Including contingency reserves in the estimate is prudent to account for unexpected expenses or shifts in project requirements down the line. Contingency funds set aside resources to handle unforeseen circumstances.
Budgeting
- Once cost estimation is complete, the next step is to develop a detailed budget plan outlining total projected expenditures, divided into line items such as materials, labor, equipment, permits, fees, overhead, and contingencies.
- The budget allocates fixed amounts of funds to each aspect of the project according to the cost estimate. This provides a clear roadmap for spending and guides financial decision-making.
- Throughout the construction process, project managers monitor actual costs against the established budget. This allows early detection of potential overages and the ability to make adjustments to stay on track financially.
- Budgets must maintain enough flexibility to accommodate changes in project scope. As requirements evolve, the budget may need revision to accurately reflect modified plans.
Additionally, accurate upfront cost estimation can reveal opportunities for potential savings without compromising project quality or goals. These insights empower stakeholders to proceed prudently, while still satisfying objectives.
Meticulous project planning
In addition to cost estimation, meticulous project planning and scheduling represent another fundamental component of preconstruction. This process involves far more than simply generating a to-do list — it means creating a comprehensive roadmap that charts the course for the entire project timeline.
Careful planning ensures resources are allocated appropriately across activities, and tasks are sequenced in a logical order to prevent delays, keep stakeholders on track, and enable the project to meet prescribed deadlines. Without a comprehensive, centralized pre-planning system, errors can surface, which represents nearly 48 percent of rework in the US. Breaking down the work into digestible phases with realistic timeframes helps managers better budget their time and resources, and ensures fewer errors in the long run.
Thorough upfront planning also helps identify potential bottlenecks, obstacles, or scheduling conflicts early on, so they can be resolved proactively. Visualizing the project's schedule and milestones enables the team to anticipate where task dependencies, resource constraints, or other issues could arise, and address them ahead of time. Detailed plans also enhance communication and collaboration by ensuring all parties understand their roles, responsibilities, and timelines clearly from the start.
Risk management
An essential pillar of the preconstruction phase is comprehensive risk analysis and management planning. During preconstruction, project teams conduct thorough assessments to identify any potential challenges, uncertainties, or risk factors that could impact the project if not addressed proactively.
These risks might stem from a wide range of sources, such as unforeseen weather events, disruptions to supply chains, changes to permits or regulations, or other external factors that could affect the project. Recognizing these potential threats early allows stakeholders to develop strategies to prevent issues from occurring or mitigate their effects if they do materialize.
An effective risk management approach also involves forming contingency plans and backup options to minimize delays and limit disruptions. Laying this groundwork during preconstruction significantly enhances the project's resilience and flexibility.
Design coordination
Early in project conceptualization, cross-functional design coordination and collaboration are instrumental in shaping the direction. This collaborative process involves synthesizing input from architects, engineers, contractors, clients, and other stakeholders to ensure the design aligns with the client's vision, while remaining realistic and feasible to execute.
Tight coordination during preconstruction maximizes the likelihood that the final design not only meets aesthetic and functional goals, but can also be successfully constructed within practical constraints. It provides the opportunity to work through any potential conflicts or constructability issues while plans are still flexible, avoiding extensive rework later.
Effective design collaboration requires clear communication between teams to navigate any needed design modifications based on budget limitations, technical requirements, or construction considerations. Addressing these adjustments proactively leads to optimal outcomes.
Value engineering
An additional opportunity in preconstruction is value engineering, which aims to maximize the value derived from each dollar invested in the project. Value engineering entails a holistic examination of the project plan to identify areas where alternative materials, methods, or design approaches could achieve comparable or superior outcomes, while enhancing efficiency or reducing costs.
The preconstruction phase offers an advantageous window to thoroughly explore these options before construction is underway. At this stage, modifications can still be made relatively easily, without causing major disruptions or delays down the line. The focus of value engineering is not solely cost reduction, but more importantly, improving overall performance, quality, and functionality in a financially responsible manner.
A collaborative, multidisciplinary approach ensures that potential value improvements are explored from all perspectives. Architects, engineers, contractors, and other experts contribute their insights to uncover optimization opportunities, leading to economical solutions without compromising quality or vision.
Ultimately, realistic cost estimation, meticulous scheduling, risk analysis, design coordination, and value engineering are the foundations of the preconstruction phase. Diligent planning and forethought during this stage enable fiscally responsible resource allocation, enhanced collaboration, proactive issue resolution, and maximized value from every dollar spent.
With a sturdy preconstruction foundation, construction teams can approach projects with the confidence that challenges will be minimized and success is primed. More importantly, with the impending construction industry slowdown in 2024, it’s vital to have a smooth-running construction project that starts with the diligence and vision established in preconstruction.